Textile Material assembling is a point by point process that transforms unrefined components into completed textures. Here is a direct manual for understanding how materials are made, beginning to end.
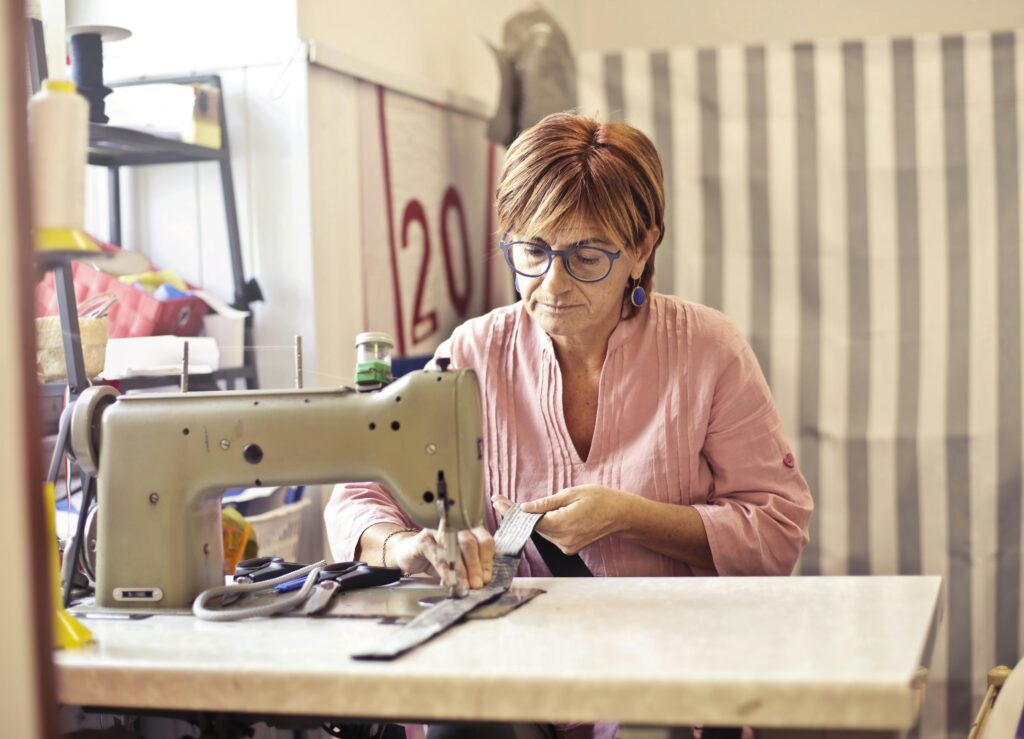
Picking the Unrefined components in textile industry
The most important phase in material assembling is choosing the natural substances. These materials can be normal filaments like cotton, fleece, and silk, or engineered strands like polyester and nylon. The decision of material influences the surface, strength, and utilizations of the last texture.
Turning the Filaments
When the natural substances are picked, they should be turned into yarn. This interaction includes cleaning and setting up the filaments prior to curving them into long strands called yarn or string. Turning machines, or spinners, finish this work by arranging and curving the filaments.
Winding around or Weaving
After the yarn is ready, it is woven or weaved into texture.
Winding around: This cycle includes intertwining two arrangements of yarns at right points. One bunch of yarns runs longwise (the twist), and different runs widthwise (the weft). The yarns are woven together on a loom to make the texture.
Weaving: In sewing, yarns are entwined to make texture. This should be possible the hard way or utilizing machines. Weaved textures will generally be more adaptable and stretchy contrasted with woven textures.
Coloring and Wrapping up of textile material
When the texture is woven or weaved, it should be colored and wrapped up.Coloring: Texture can be colored in a scope of varieties and examples. Coloring can occur at various stages, for example, before the texture is made into clothing (yarn coloring) or after it’s been made into a piece of clothing (piece coloring).
Wrapping up: This incorporates different medicines to improve the texture’s properties. For instance, completing cycles can make the texture gentler, more strong, or water-safe. It might likewise include adding surfaces or examples.
- Cutting and Sewing
The subsequent stage is cutting the texture into pieces and sewing them together to make articles of clothing or other material items. This is many times done utilizing examples and formats to guarantee that each piece is the right size and shape. Sewing machines are utilized to consolidate texture pieces. - Quality Control
Before the end results are conveyed, they go through quality control checks. Assessors analyze the texture and completed things for deformities or irregularities. This step guarantees that the items satisfy the necessary guidelines and are prepared for use or deal. - Bundling and Circulation
At last, the finished material items are bundled and ready for circulation. This includes naming, pressing into boxes, and transportation to retailers or clients. Appropriate bundling safeguards the items during transport and capacity.
What are the main raw materials used in textile manufacturing?
The main raw materials in textile manufacturing include:
- Natural Fibers: Such as cotton, wool, silk, and linen. These fibers come from plants or animals and are valued for their comfort and breathability.
- Synthetic Fibers: Such as polyester, nylon, and acrylic. These are made from chemical processes and are known for their durability and resistance to wrinkles and stains.
- Blended Fibers: Combinations of natural and synthetic fibers to combine the benefits of both.
2. What is the difference between weaving and knitting in textile production?
- Weaving: This process involves interlacing two sets of yarns (warp and weft) at right angles to create fabric. Weaving produces a variety of fabric types, including plain weave, twill, and satin.
- Knitting: Involves looping yarns together to form a fabric. Knitted fabrics are generally stretchier and more flexible compared to woven fabrics. Knitting can be done using hand techniques or machines.
3. How is fabric dyed during the manufacturing process?
Fabric dyeing can occur at different stages:
- Yarn Dyeing: Where yarns are dyed before being woven or knitted into fabric. This allows for uniform color throughout the fabric.
- Piece Dyeing: The fabric is dyed after it has been woven or knitted but before it is cut and sewn into garments. This method is used for producing large quantities of fabric in specific colors.
- Garment Dyeing: The finished garments are dyed, allowing for small batches of custom colors.
4. What are common finishing techniques used in textile manufacturing?
Finishing techniques enhance the properties and appearance of fabric. Common techniques include:
- Softening: To make the fabric softer and more comfortable.
- Waterproofing: Applying treatments to make the fabric resistant to water.
- Texturizing: Adding patterns or textures to the fabric surface.
- Antimicrobial Treatments: To reduce the growth of bacteria and odors.
5. How does quality control fit into the textile manufacturing process?
Quality control is a crucial step in textile manufacturing to ensure the final products meet standards:
- Inspection: Fabrics and garments are checked for defects, such as irregularities in color, texture, or stitching.
- Testing: Fabrics are tested for durability, colorfastness, and other performance factors.
- Consistency: Ensuring that all products adhere to the specified quality standards and specifications before they are packaged and shipped.
These FAQs provide a clear overview of key aspects of textile manufacturing, helping to understand the steps involved in producing textiles from raw materials to finished products.